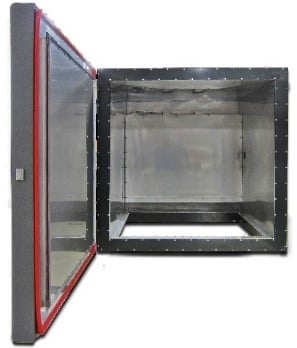
Thermal Chamber Applications
Whether you need to test or condition at MIL-STD or beyond, Sigma Systems can provide the optimal thermal environment. Hundreds of designs comprise our applications library accommodating test setups from satellite antennas to implantable stents, from aircraft landing systems to batch testing thousands of LEDs, and from calibrating cameras and MEMS devices to quality testing down hole drilling instrumentation.
Every thermal chamber is optimized for size, visual and physical device access, temperature range, and transition rates.
Application Examples
• Down hole instrumentation quality testing
• Network equipment characterization
• Flow transmitter production testing using multiple zones
• High temperature testing with access from three sides
• Medical device manufacturing integration
• Automotive component accelerated life testing
• Other important applications
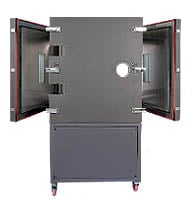
Network equipment characterization
This 26 cu. ft. thermal chamber has dual access for equipment characterization with a large rack mounted DUT (thermal load 2 x 150lb DUTs dissipating 2 kW each). The inclusion of notches on the left side and an aperture on the right side help remedy complex cabling issues.
Integrating Temperature with Tensile Testing
Chambers and temperature forcing systems can be designed with apertures, ports, and pass-throughs to integrate directly into an existing tensile test setup. Temperature ranges from -185 to 500°C satisfy both high and low temperature testing for ASTM and MIL-STD requirements.
Materials testing often requires a long and narrow cavity to accommodate measurement devices. With tensile testing, objects are pulled in one direction and stressed until failure, but strain can also be used to pull the object in both directions. Customizing chambers for the OEM and end-user is what we do best.
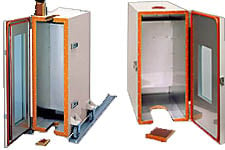
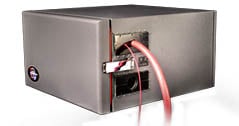
Telemetry system testing using LCO2
This chamber provides a temperature environment for defense telemetry equipment requiring LCO2 as the cooling medium, while minimizing CO2 emission. Sigma Systems-designed notch inserts fit customer’s test cables and prevented LCO2 from escaping. These notches make loading and unloading DUTs easier, and therefore throughput was increased by reducing test setup time.
Aircraft electronics test integrated with existing vibration table
A 28” x 28” aperture designed in the floor of this chamber integrates with customer’s existing vibration table by acting as a hood over the test specimen. This chamber has rapid temperature transition rates of > 35°C/min going hot, and > 15°C/min going cold.
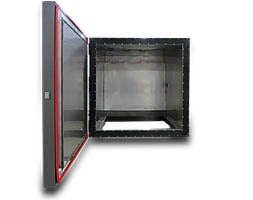
Telecom equipment design verification testing
The hole pattern in the floor and ceiling of this chamber secures the rack-mounted equipment for the device under test (DUT). Customer challenges with routing cables to the rear of the system were addressed with a cable notch, allowing for easier loading and unloading of the DUTs in the workspace.
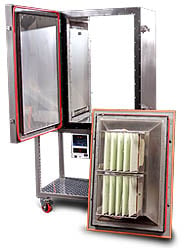
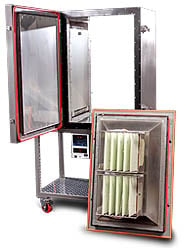
MEMS device calibration testing
This chamber provides a specified temperature range of -60°C to +130°C and a gradient of less than +/- 1.3°C. A card cage fixture can be first loaded onto a rear, pull off door before the door is re-attached. The customer can prepare the next test, and once the current test is finished, is able to simply open the front, hinged door and switch out the tested cards for new ones. This dual access maximizes throughput and allows for the testing of over 2,500 MEMS per test.
LED extended life testing
These stacked chambers meet specified throughput requirements by batch testing over 600 LEDs using eight cryogenic thermal platforms per chamber. These thermal platforms act as active heat sinks to dissipate heat away from the DUTs during testing. Throughput is further increased between tests with the inclusion of two doors and apertures, while stacking the chambers produces a smaller footprint.
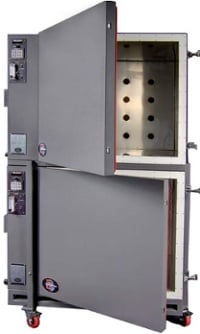
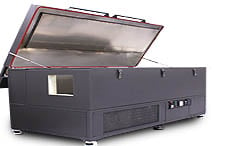
Down hole sensor and instrumentation quality testing
This compressor-based thermal chamber is capable of housing unusual sized DUTs (5-7’ long, 200lbs+) that can handle 200+°C for a quality test. Chamber(s) can be bolted together in series to accommodate for longer and interconnected DUTs. Openings in the chamber walls make loading longer DUTs through multiple chambers easier.
Flow transmitter production testing using multiple zones
This multi-zoned chamber provides separately controlled temperature environments with increased test access. The center zone stresses the sensor assembly by simulating hot fluid temperatures. The end chambers stress sensor electronics to simulate ambient temperature extremes.
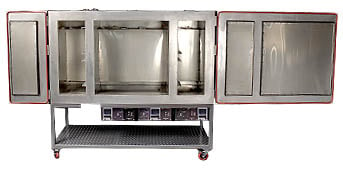
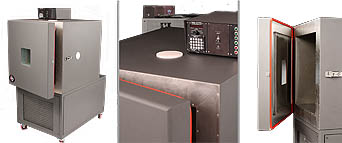
High temperature testing with access from three sides
This chamber for materials testing is conducted at 300°C using only compressor cooling, per customer’s request. An aperture on the top, left and right side of the chamber allow for easier cable access. A window and interior lighting provide the needed visibility requirement during testing.
Medical device manufacturing integration
A remote refrigeration package permits this chamber to integrate with an existing robotic manufacturing process. Non-textured paints and Teflon apertures were used to comply with the clean room compatibility requirements. The connecting hose added low temperature insulation to prevent thermal losses.
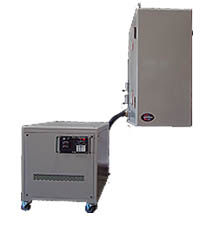
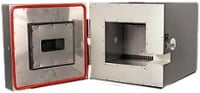
Automotive component accelerated life testing
This bench top chamber is capable of performing accelerated life testing at a specified temperature range of -185°C to +350°C, with transition rates of approx. 20°C per minute. This design included 4” walls to minimize heat loss at temperature extremes. High-efficiency insulation allowed this chamber to reach +350°C, with a built-in window, and bench top setup. Normal temperature limitations for 4” thick insulated walls would be +185°C and would not allow for a window.